Hydraulic System Maintenance Checklist and Tips
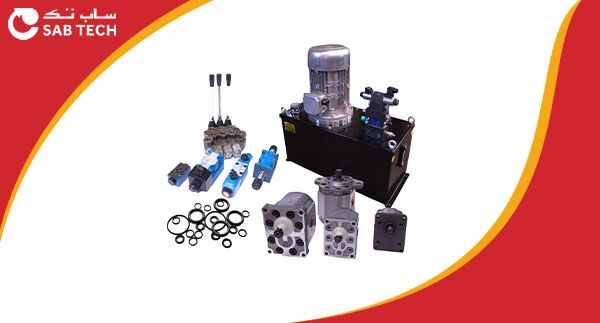
Practically any heavy equipment used across diverse industries is operated through hydraulic power. From cargo lifts to car washes and high-security road blockers to compactors and balers, the force generated by a hydraulic system enables them to effortlessly perform tasks that require high levels of lifting, pushing, or moving power.
Hydraulic systems themselves are made up of various components that work together to generate the power. The most vital of these is the hydraulic fluid or hydraulic oil. Apart from the fluid a hydraulic system includes hydraulic fluid tanks, pumps, actuators, valves and seals, hoses and pipes, filters, accumulators, and pressure gauges and sensors.
For any hydraulic powered machinery to perform optimally, the hydraulic system needs to be maintained in prime condition. In this blog, we have compiled a hydraulic system inspection checklist and take you through various hydraulic system maintenance tips.
Importance of Hydraulic System Maintenance
- Equipment Life: Heavy machineries are expensive and must be treated with care. Carrying out both preventive and corrective hydraulic system repair and maintenance prolongs the life of the equipment, enhancing its productivity and slowing its depreciation rate.
- Worker Safety: When working with hydraulic systems, the safety of workers is of paramount importance. Improperly maintained hydraulic machinery can cause equipment malfunction, fluid leak and ejection at high pressure and temperature, fire and explosion, all of which can result in serious accidents, even leading to loss of life.
- Prevent Operational Delays: Lack of proper hydraulic system maintenance can result in more frequent breakdown of operations, leading to unwanted delays that can put severe pressure on time-sensitive tasks and cause loss of business.
- Save Unnecessary Expenses: Timely maintenance of hydraulic systems can save businesses from incurring heavy costs in repairing or replacing damaged parts, that are often very expensive.
Hydraulic System Maintenance Checklist
- Hydraulic fluid maintenance: As mentioned earlier, the hydraulic fluid is the most vital component of the hydraulic system. Carry out periodic checks to ensure that the fluid is at the right level, the right temperature, and free of contaminants. Use implements like dipsticks and gauges to inspect the level and quality of the fluid. Low fluid levels can damage the pump, and if the fluid is contaminated, implement a full system purge and replace with fresh, clean oil.
- Filter inspection and change: Filters keep the fluid circulating through the hydraulic system clean and free of particulate matter. However, over time they can get clogged, reducing their effectiveness, which can lead to equipment malfunctions. Therefore, check filters regularly and change them frequently.
- Check valves and seals: All valves and seals should be regularly checked to ensure that they are not loose or cracked. Damaged or untightened valves and seals can expose the hydraulic system to the outside environment, leading to buildup of dust and moisture which can corrode the components. Clean all components with a cloth and vacuum cleaner thoroughly, tighten valves and replace damaged seals. Clean the breather regularly to prevent moisture and replace breather filters and caps on a periodic basis.
- Inspect hoses and pipes: Leaks or obstructions within the pipes and fittings of a hydraulic system can have catastrophic results such as explosions and fires. Carry out a careful visual inspection of all hoses and pipes and their connectors to ensure that there are no holes, dents, corroded, bent or distended portions. Make sure that all pipes and hoses properly fit into their corresponding components. Hose lines should also be checked to ensure that they are free of any entanglement. Immediately replace or repair any pipe or hose that displays signs of possible damage.
- Test pressure and flow: Pressure and flow are the two most important aspects of a hydraulic system. If they are too high, they can impact the entire system including the pump, the actuator, the pipes, and the valves, leading to bursting and explosion. Very low pressure and flow can lead to overheating and equipment malfunctions. Use pressure gauges and flow meters to constantly monitor and calibrate the system for optimal pressure and flow levels.
Important Hydraulic System Maintenance Tips
- Use your eyes and ears: Maintenance staff should visually inspect all the components of the hydraulic system for presence of air bubbles, frothy fluid and signs of damage. Often, listening carefully to the system can also reveal problems that cannot be seen. Listen for unusual sounds such as gurgling, whistling, rattling, or strange vibrations.
- Use proper tools and testers: Use tools and testing equipment specifically designed for hydraulic system performance optimization such as pressure gauges, flow meters, testers for sediment and viscosity, thermometers, scanners, etc. Always check your readings against manufacturer specifications and don’t make too many adjustments if they are not required.
- Always wear protective gear: Practice safety when inspecting or carrying out maintenance activities. Always wear gloves, goggles, and other personal protective equipment (PPE) when handling hydraulic system components.
- Implement lookout/tagout procedures: Lookout and tagout procedures, known as LOTO are mandatory safety procedures that need to be implemented while carrying out maintenance activities on a hydraulic system. For example, ensure that the hydraulic system is properly depressurized before inspection, and prominently mark equipment with warning signs that are undergoing maintenance to prevent accidental use.
- Follow manufacturer’s instructions: Always follow the recommended steps and procedures laid out in the manufacturer’s maintenance handbook or guide. Do not try to take any action that has not been specifically stated in the instructions.
- Establish and follow emergency safety protocols: In case of any emergency situation arising due to malfunctions in the equipment, follow the mandated safety protocols for shutting down the system and evacuating the premises.
Conclusion
Hydraulic system maintenance is a crucial and mandatory exercise that keep hydraulic powered machinery from malfunctioning or causing serious accidents. Periodically scheduled maintenance improves the life and operability of the machinery, prevents delays, and saves costs. Hydraulic system maintenance is a dangerous operation that must be carried out in a systematic and thorough manner by trained professionals, following manufacturer’s instructions and safety protocols.
About SAB TECH
SAB TECH is a leading manufacturer and distributor of high-quality hydraulic machinery, equipment and spare parts in Saudi Arabia. The company invests heavily in research and development of cutting-edge hydraulic systems technology, aimed at enhancing the efficiency, sustainability and safety of their products, which include hydraulic-powered washing and lifting, waste and recycling, perimeter protection, and loading system equipment. Talk to their experts today to find out how their expertise is hydraulic power technology can benefit you.